Flat roofing is a popular option among commercial buildings, providing property owners an affordable and reliable way to protect their business assets. From various materials to the pros and cons that they provide for your facility, there’s a lot to understand about commercial flat roofing.
This guide explores the basic concepts, varying costs, the benefits of choosing flat roofing for commercial buildings, different roofing material options, the process of installation, and more. Let’s plunge into the world of commercial flat roofing.
An Introduction to Commercial Flat Roofing
Commercial flat roofing refers to roofs with a slight pitch, usually between 1/4 to 1/2 inch per foot, which is just enough to allow water runoff. This architectural design maximizes usable space on the roof, which can be used for systems like HVAC units or even as a green space. At its core, commercial flat roofing aims to balance cost-efficiency and functionality in a commercial setting.
Flat roofs are supported by roofing felts, metal decks, or concrete, and are sealed with various types of membrane systems to prevent water ingress. From EPDM to Modified Bitumen, these membranes ensure the roof can withstand elements and foot traffic while offering puncture resistance and energy efficiency.
Understanding the Costs of Commercial Flat Roofing
The cost of commercial flat roofing can vary widely, depending on several factors, including material choice, installation complexity, and geographic location. Generally, prices for standard single-ply membrane systems can range from $4 to $8 per square foot. More robust systems, like built-up roofing (BUR) or premium heavy-duty composite systems, might push the price to around $13 per square foot.
Investing in long-term maintenance and potential energy savings is crucial. Some roofing materials, such as reflective membranes, can significantly reduce cooling costs, making them a wise investment over time. Consulting with an experienced roofing contractor can help pinpoint the best option for your budget and needs.
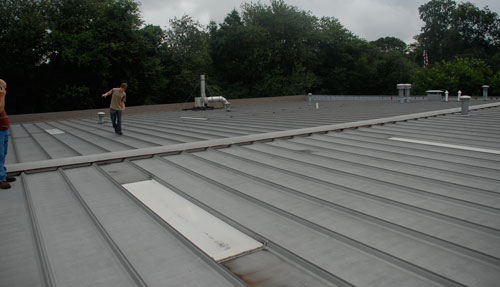
Why Choose Flat Roofing for Commercial Buildings?
Flagging down reasons to opt for commercial flat roofing isn’t hard. Flat roofs are considerably less expensive to install and maintain than their sloped counterparts. The low maintenance is a big win for building owners looking to minimize overhead costs.
Additionally, flat roofs provide extra space for HVAC units, solar panels, or even roof gardens. This versatility not only boosts the functionality of your commercial property but can also contribute to its energy efficiency and aesthetic appeal. Moreover, flat roofing systems are known for their durability and robustness, especially when well-maintained.
Different Types of Commercial Flat Roofing Materials
The choice of roofing material plays a pivotal role in the longevity and performance of commercial flat roofs. Each material offers unique benefits and fits different budgetary and climatic needs. Here’s a closer look at some of the most popular materials in the roofing industry.
Built-Up Roofing (BUR)
Built-up roofing, or BUR, is one of the oldest and most reliable methods. It’s constructed from multiple roofing felts sandwiched between bitumen (asphalt) layers. A top layer, often a gravel or cap sheet, provides UV protection and fire resistance.
BUR systems are revered for their durability, simple roof repairs, and resistance to foot traffic. With costs between $4 and $10 per square foot, you can expect this type of commercial flat roofing material to last between 15 and 30 years.
Modified Bitumen Roofing
Modified Bitumen takes the traditional BUR approach and enhances it with modern polymer technology, improving its flexibility and temperature tolerance. This system, usually applied in two layers—a base sheet and a cap sheet—offers great tensile strength and puncture resistance.
Modified bitumen roofing is often chosen for its ease of repair and heat-welded seams that boost waterproofing capabilities, flexibility, and durability. At only $4 to $8 per square foot, it’s also highly affordable, considering its 15 to 30-year lifespan.
EPDM Roof Membrane
EPDM (Ethylene Propylene Diene Terpolymer) roofing is celebrated for its outstanding durability, longevity, and environmental resistance. This synthetic rubber roofing membrane system is fully adhered, mechanically attached, or ballasted, making it versatile for various roof surfaces. Its black color helps melt snow and ice, a feature appreciated in colder climates.
You may pay a little extra for this flat roof material, at $5 to $13 per square foot, but its 40 to 50 years longevity is well worth the investment.
PVC Roof Membrane
PVC roofing membranes are known for their strength, performance, and fire resistance. These membranes are heat welded at seams, creating a monolithic, watertight layer over the roof surface. PVC’s chemical composition also provides excellent resistance to chemicals and is an ideal choice for restaurants and other businesses that emit fats and oils through ventilation systems.
PVC roofing materials range from $6 to $10 per square foot, with an average lifespan of 20 to 30 years.
TPO Roof Membrane
TPO (Thermoplastic Polyolefin) roofing combines the best features of EPDM and PVC membranes, offering high reflectivity, flame resistance, and energy efficiency. TPO’s lightweight, flexible sheets are heat welded at the seams, providing exceptional durability and seam strength. Its ease of installation and low maintenance requirements make it popular among building owners and professionals.
TPO roofing is extremely affordable, with costs ranging between $3 to $7 per square foot and a lifespan of 15 to 30 years.
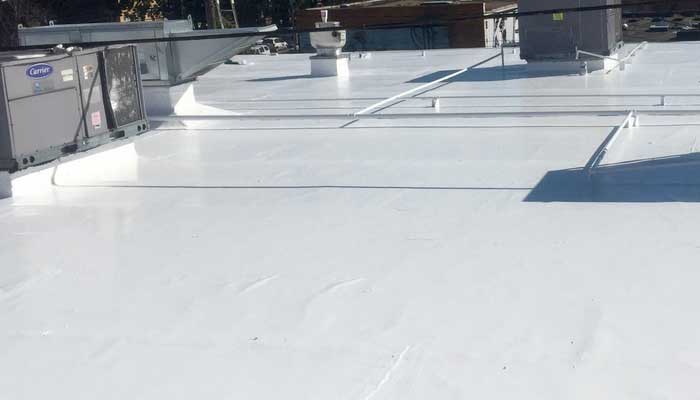
The Process of Installing a Commercial Flat Roof
Installing a commercial flat roofing system is a straightforward process that professional contractors can implement seamlessly. While the exact steps may vary from project to project, you can expect some variation of the following:
Site Preparation
Before installation can occur, a bit of groundwork is necessary. Site preparation for commercial flat roofing involves clearing the deck of debris, ensuring it’s dry and smooth. This step is crucial because bumps or moisture can spell trouble for the new roof. A thorough inspection for structural integrity ensures the building can support the roof system. Skipping this step could lead to complications down the line.
Next up, setting up safety measures is a must. This includes installing guardrails and safety nets if necessary. Ensuring the safety of workers is paramount in any roofing project. Additionally, planning for efficient water drainage from the get-go is essential. Flat roofs aren’t entirely flat; they have a slight slope to prevent water accumulation. This slope needs to be calculated and implemented during the preparation phase.
Installation Process by Roof Type
The installation process varies depending on the type of roofing material chosen. For instance, installing an EPDM roofing system involves rolling out the rubber membrane, ensuring it’s free from wrinkles, and adhering it to the roof surface. Depending on the building owner’s preference and the roof’s specifications, this could be either mechanically attached or fully adhered.
On the other hand, modified bitumen roofs are a reliable option for buildings requiring high puncture resistance, such as those with heavy foot traffic. Its installation involves torching down bitumen layers, interspersed with fiberglass or polyester-reinforced cap sheets. This creates a durable, resistant coating that’s hard to beat.
Meanwhile, TPO and PVC roofing systems use heat welding for a sealed, continuous surface. The membrane sheets are overlapped and heat-welded, creating a watertight, highly durable roof system. These roofing types are known for their energy efficiency, a big plus for eco-conscious building professionals.
While the process may vary slightly from material to material, working with a qualified roofing contractor ensures the job is done properly.
Post-Installation Procedures
After the main event, post-installation procedures can ensure longevity and performance. Initial checks involve looking for installation errors, ensuring all membrane seams are properly sealed, and verifying that flashings are correctly installed and secured. A professional roofing contractor might conduct a water test to check for leaks.
Maintenance plans are then drawn up. These typically include regular inspections, cleaning to prevent debris build-up, and immediate repair of minor issues to avoid future headaches. With proper maintenance, commercial flat roofs can have an impressive lifespan, saving building owners from frequent reroofing costs.
The Advantages and Disadvantages of Commercial Flat Roofing
While commercial flat roofing provides a generally positive impact, it’s without its share of challenges. Let’s explore some of the advantages and disadvantages of flat roofing.
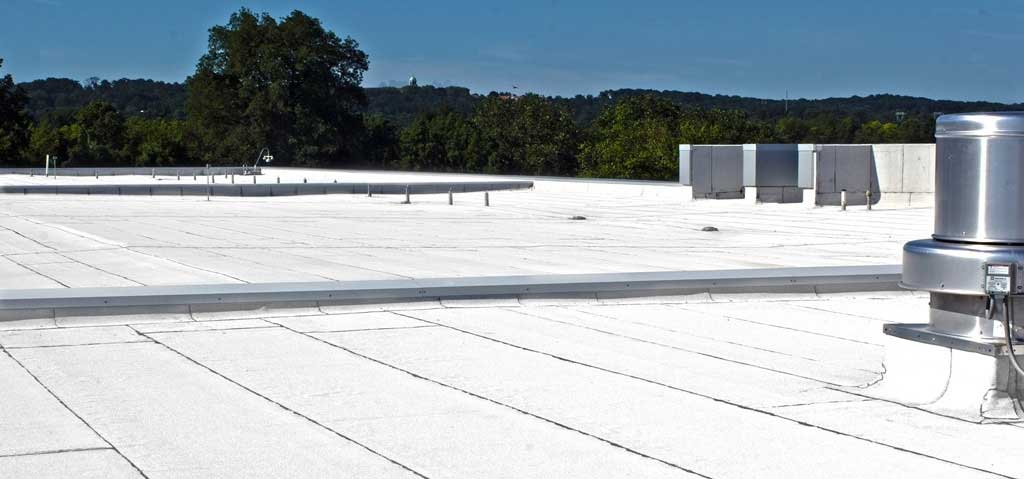
The Advantages of Flat Roofing
Commercial flat roofing offers many benefits, such as:
- Cheaper Installation and Maintenance – Commercial flat roofs are generally less expensive than sloped roofs. They’re easier to access for maintenance and repair, keeping long-term costs down.
- Energy Efficiency – Flat roofs can support energy-efficient solutions like vegetative roofs or cool roofing materials, lowering utility bills.
- Flexibility in Use – The flat surface provides additional space for HVAC units, solar panels, or rooftop gardens. This adaptability makes commercial flat roofs particularly appealing for certain types of buildings.
These benefits make flat roofing a compelling choice for many building owners. However, like any roofing option, there are also potential drawbacks.
The Downsides of Flat Roofing
Flat commercial roofing systems are likely to present challenges for your facility as well, including:
- Drainage Issues – Without proper drainage, water can pool and lead to leaks and structural damage. Complex drainage systems are often necessary to combat this.
- Shrinkage and Weight Distribution – Roofing materials might shrink over time, causing gaps and leaks. Also, flat roofs might not distribute weight as efficiently as slope roof systems, potentially causing sagging if not properly designed.
- Susceptible to Damage – While properly installed flat roof systems are fairly durable, they can become damaged if not regularly maintained and inspected.
How long does a commercial flat roof last?
Lifespan varies significantly based on the materials used and maintenance practices. On average, commercial flat roofs last between 15 to 25 years. Regular inspections and maintenance can push the higher end of this range, especially with materials known for longevity, such as PVC or TPO membrane systems.
How much does commercial flat roofing cost?
Costs can range widely depending on the roof size, materials chosen, and the region. Generally, prices might span from $4 to $13 per square foot. With added features for energy efficiency or premium heavy-duty composite materials, costs can increase but might be offset by long-term savings in energy and maintenance expenses.
Are flat roofs more prone to leaks?
While any roof can develop leaks, proper installation and maintenance can significantly mitigate these risks for flat roofs. Issues arise primarily from neglect, especially regarding drainage and regular checks for wear and tear. With proactive care, flat roofs can be just as reliable as their sloped counterparts.
Choose a Roofing Company You Can Trust
Look no further than Alpha Commercial Roofs for all your roofing needs. Our team of professional and experienced workers will ensure that you have the best roof to combat any situation.
Contact us today at 855-862-7663